The Vital Duty of Container Welding Examination in Ensuring Structural Integrity and Safety And Security Conformity in Industrial Applications
In the world of commercial applications, storage tank welding inspection becomes a crucial aspect in guarding architectural stability and guaranteeing conformity with security laws. Utilizing a mix of techniques such as aesthetic evaluations and advanced testing methods, these inspections serve to determine and mitigate potential flaws before they intensify right into considerable threats. The ramifications of these techniques expand beyond simple regulatory adherence; they basically impact operational efficiency and asset durability. The complexities surrounding the assessment procedure motivate a closer assessment of its methodologies and outcomes, revealing layers of importance that merit further exploration.
Significance of Container Welding Evaluation
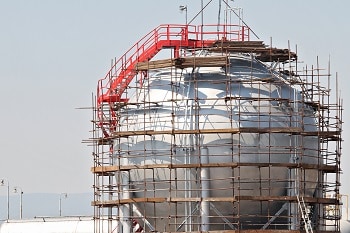
Making sure conformity with industry requirements and regulations is one more substantial element of container welding evaluation. Regulative bodies mandate strict standards for the building and upkeep of storage containers, and thorough evaluations aid organizations stick to these needs. Non-compliance can cause severe penalties, consisting of penalties and shutdowns, even more emphasizing the requirement for extensive assessment procedures.
Additionally, storage tank welding evaluation plays a vital role in preserving functional effectiveness. In recap, the relevance of container welding assessment exists in its capacity to safeguard public wellness, safeguard the environment, and make sure conformity with regulatory structures.
Key Assessment Methods
Effective container welding evaluation counts on a variety of essential techniques that ensure detailed assessment of weld quality and architectural honesty. Among the most common methods are visual evaluation, ultrasonic testing, radiographic screening, and magnetic bit screening - Tank Welding Inspection. Each technique offers distinct advantages in evaluating different aspects of the weld
Visual examination acts as the very first line of protection, allowing inspectors to recognize surface area defects, abnormalities, or inconsistencies in the weld bead. Ultrasonic screening utilizes high-frequency audio waves to identify internal imperfections, such as cracks or voids, offering a thorough assessment of weld honesty. This method is especially efficient in finding issues that may not be noticeable externally.
Radiographic screening utilizes X-rays or gamma rays to produce photos of the welds, disclosing internal suspensions and giving a permanent record for future recommendation. This strategy is highly effective for essential applications where the danger of failure need to be minimized.
Finally, magnetic bit screening is used to determine surface and near-surface problems in ferromagnetic materials. By using electromagnetic fields and great iron fragments, assessors can pinpoint interruptions that may endanger the structural stability of the container. With each other, these techniques form a robust framework for guaranteeing high-grade welds in industrial applications.
Conformity With Security Standards
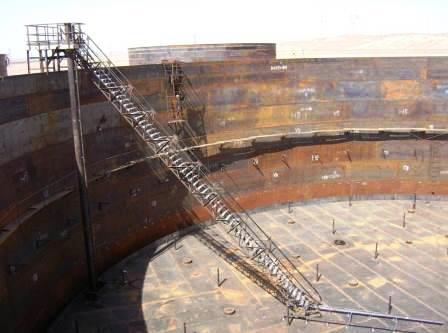
Routine examinations play an essential duty in making certain conformity by identifying possible failings or variances from recommended standards. Inspectors are trained to evaluate weld high quality, verify product specs, and analyze the general structural honesty of storage tanks. Their know-how is important in ensuring that welding procedures fulfill the needed safety standards.
In addition, conformity with safety requirements not only safeguards workers however likewise safeguards the environment from possible hazards such as leakages or devastating failures. Organizations that focus on safety and security conformity are much better positioned to reduce threats, boost operational efficiency, and cultivate a society of security within their workforce. In recap, preserving extensive conformity with safety and security standards is vital for the successful procedure of container welding tasks in industrial setups.
Advantages of Routine Examinations
Normal inspections are essential to preserving the architectural stability and security of bonded storage tanks. These inspections offer a systematic technique to determining prospective problems or weak points in the welds, making certain that any kind of problems are dealt with before they intensify right into significant failures. By performing regular evaluations, organizations can detect corrosion, exhaustion, and various other types of degeneration that might jeopardize tank efficiency.
Moreover, constant examinations contribute to conformity with get redirected here industry laws and requirements. Complying with these guidelines not only alleviates lawful risks yet additionally boosts the company's online reputation for security and integrity. Routine assessments cultivate a proactive security society, urging employees to recognize and prioritize the value of tools integrity.
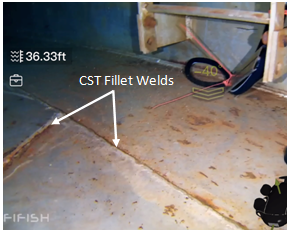
Case Researches and Real-World Applications
Situation research studies and real-world applications show the concrete effect of effective container welding assessment practices. One notable example is a big petrochemical center that faced considerable functional disturbances as a result of leaks in tank. Adhering to the application of extensive welding assessment procedures, consisting of aesthetic and ultrasonic screening, the facility determined vital defects in weld seams that could have brought about catastrophic failings. This aggressive strategy wikipedia reference not just avoided environmental hazards yet also saved the firm millions in possible cleanup expenses and governing fines.
Similarly, a water treatment plant applied a detailed inspection program for its tank welding procedures - Tank Welding Inspection. By incorporating non-destructive screening methods, the plant had the ability to identify early indicators of corrosion and tiredness in weld joints. This prompt intervention expanded the life expectancy of the containers and ensured conformity with security laws, thus securing public health
These study underscore the you could look here value of normal and methodical tank welding assessments. By focusing on these methods, markets can alleviate threats, boost structural stability, and make certain compliance with safety criteria, inevitably leading to enhanced functional efficiency and decreased responsibilities.

Conclusion
In conclusion, tank welding inspection is an important component of preserving architectural stability and safety and security in industrial applications. Using numerous evaluation strategies guarantees very early detection of possible imperfections, consequently stopping devastating failures.